When there’s no space for a full-size crusher, a Hartl HBC 950 Crusher Bucket is just the job for JPE Aggregates.
Back to all News ArticlesMidlands, United Kingdom
19th November 2019
0 comments
When there’s no space for a full-size crusher, a Hartl HBC 950 Crusher Bucket is just the job for JPE Aggregates.
Crushers
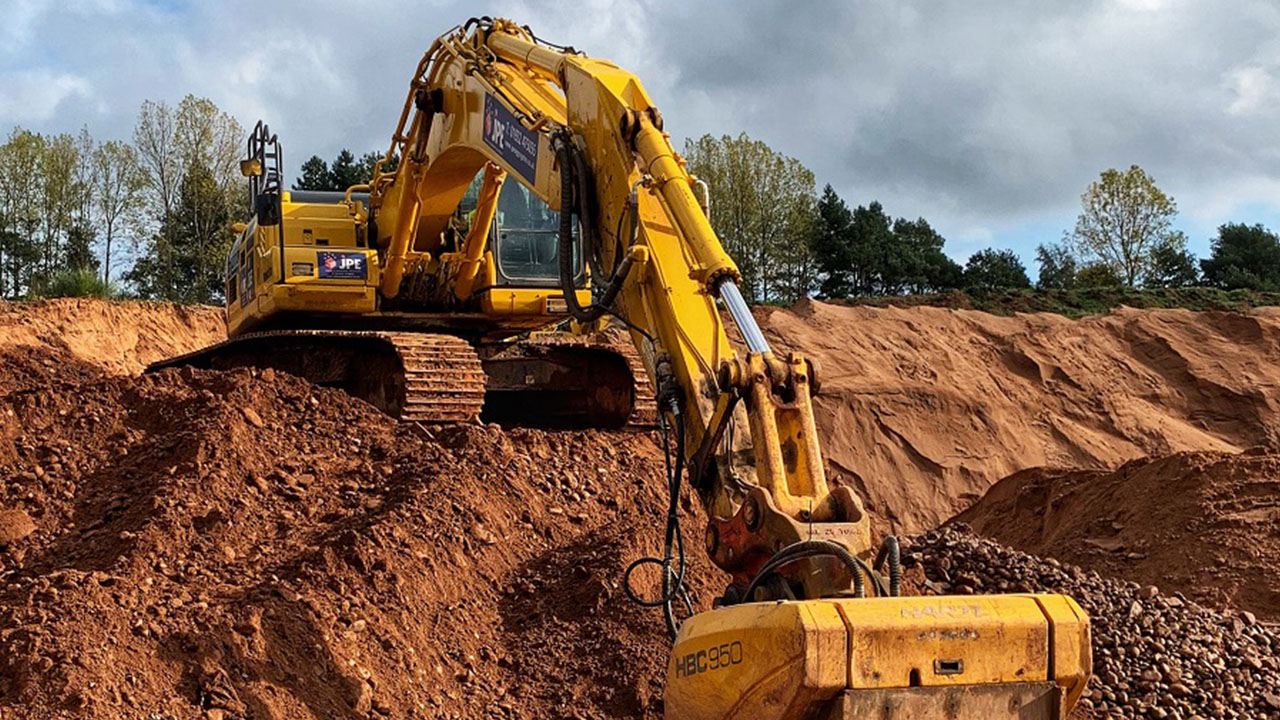
JPE is one of the Midlands leading suppliers of aggregates, sand and soils to the construction industry. The business operates a number of strategically located sites from which it provides virgin, washed and unwashed recycled aggregates together with inert waste disposal, exempt from Landfill Tax. The business has been in existence for over 20 years, developing a reputation for providing the highest levels of service and a commitment to supporting sustainability in the construction industry.
The company has been involved in many of the leading projects in the Midlands area, including the Black Country Route, Trent Valley Four Tracking Project (TV4), the M6 Toll Road and the M6 hard shoulder strengthening.
The main objective of JPE’s Seisden Quarry in Wolverhampton is the production of sand. The material is taken from the quarry and directly loaded in to a wash plant, which both separates and washes the material in to saleable products, including a much sort after 0-2mm building sand and 0-4mm sharp sand, as well as three sizes of aggregate. Extracted from the plant, however, is the +60mm oversized which is both hard rock and sandstone. The overburden has been building up for a number of years with it not being a saleable product. JPE’s Managing Director Steve Birch explains “The oversized was being stockpiled at the site and the challenge was how to turn that into a saleable product. Of course, we could use a crusher, but we tend to do that on a campaign basis, meaning we had to wait until we had 10,000 tonnes. We simply don’t have the room to stock 10,000 tonnes on this site.”
The bucket was brought in to enable the business to crush the currently unsaleable oversized from the wash plant. Once the material is crushed, it is returned to the wash plant, creating both aggregates and the much sort-after sand. The bucket is enabling the business to crush daily rather than on a campaign basis, meaning stockpiles are kept to a minimum in key areas of the quarry. Furthermore, the process is being undertaken by a single man and a single machine, as opposed to a crusher which requires more capital equipment and human resources.
Customer Comments:
“The bucket is doing an excellent job creating saleable product from the overburden which had been building up within the quarry. The throughput is very impressive, and due to the ‘figure of 8’ motion of the jaws, the bucket stays clean even under damp conditions.” Steve Birch, JPE Managing Director.
“We feel the bucket is doing at least as good a job as any mobile crusher. It’s also an adaptable bit of kit, having crushed concrete and tarmac to plainings since we’ve had it.” Ben Dixon, JPE Assistant Quarry Manager
""
We feel the bucket is doing at least as good a job as any mobile crusher. It’s also an adaptable bit of kit, having crushed concrete and tarmac to plainings since we’ve had it.
Ben Dixon, JPE Assistant Quarry Manager
News
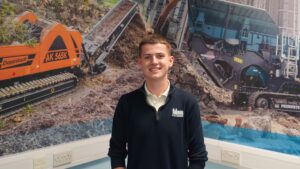
Ben Dickson’s Apprenticeship Success
At Blue Spares, we’re proud to support career growth through apprenticeships. Ben Dickson joined...
Find Out More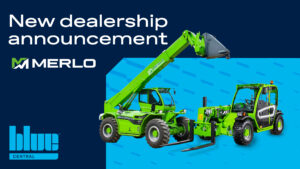
Blue Machinery (Central) Appointed as Official Merlo Dealer
Blue Machinery (Central) Ltd is excited to announce its recent appointment as an official...
Find Out More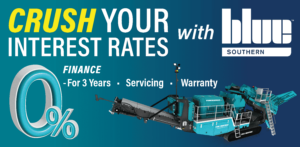
Crush your Interest Rates with 0% Finance
Boost your business with 0% INTEREST on NEW POWERSCREEN Crushing and Screening machines. Blue...
Find Out More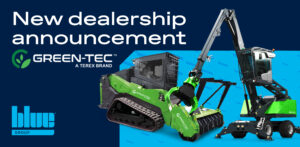
Blue Machinery appointed as exclusive UK dealer for Terex Green-Tec
Blue Machinery, a leading provider of materials processing and handling equipment, is proud to...
Find Out More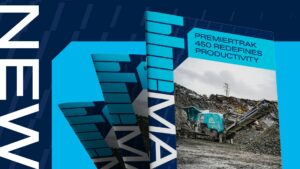
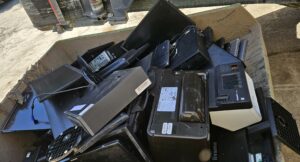
Blue’s Commitment to Recycling IT Equipment
In today's rapidly evolving technological landscape, Blue Machinery constantly upgrades their IT...
Find Out More
Strategic Restructuring at Blue Machinery (Scotland) Ltd
As part of a team restructuring, Blue Machinery (Scotland) Limited have announced several strategic...
Find Out More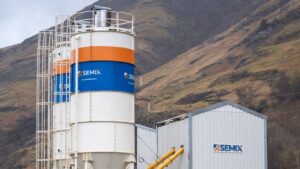
Blue Scotland expand into Concrete Batching Plants
Blue Machinery (Scotland) Ltd are delighted to announce that they are now the authorised...
Find Out More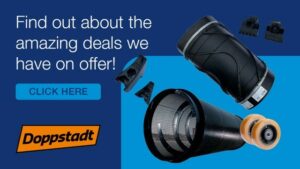
Take a look at the latest deals available at Blue Spares!
RECIEVE A £100 AMAZON VOUCHER WITH EVERY TROMMEL DRUM PRUCHASE Looking for a new drum for your...
Find Out More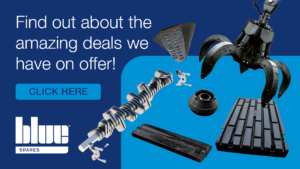
Take a look at the latest deals available at Blue Spares!
FREE £50 VOUCHER WITH ANY SET OF MANGANESE PURCHASED Purchase any set of jaw plates, concave...
Find Out More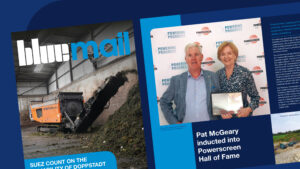
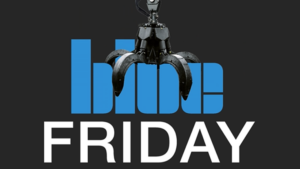
Blue Friday Deals!
We are running a number of deals in the lead up to Blue Friday! Here is a list of what we have...
Find Out More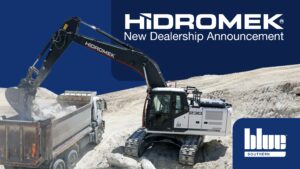
Blue Southern appointed as Hidromek Dealer
Blue Machinery (Southern) Ltd is delighted to announce their appointment as the Hidromek dealer for...
Find Out More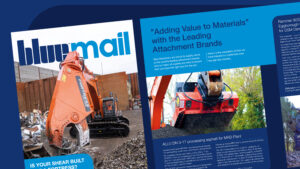
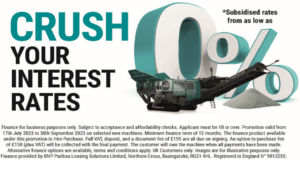
0% finance available on new Powerscreen machines
Crush your interest rates! Subsidised rates available from as low as 0% on selected Powerscreen...
Find Out More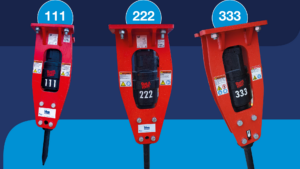
WE’RE GIVING AWAY A FREE RAMMER HAMMER
WE'RE GIVING AWAY A RAMMER HAMMER! Enter here: https://bit.ly/3VolJ5T As you may have seen...
Find Out More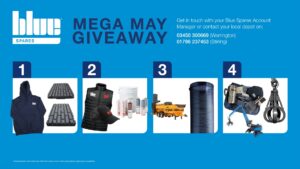
MEGA MAY GIVEAWAY
Throughout May we are running four promotions to give you the chance to get your hands on some FREE...
Find Out More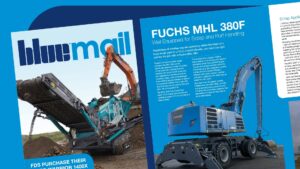
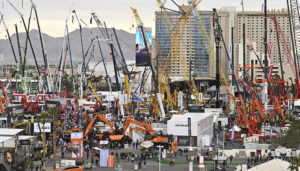
Record breaking Con-Expo/ Con-Agg Trade Show
Con-Expo/Con-Agg 2023 drew in a record breaking 139,000 visitors to the Las Vegas event, making it...
Find Out More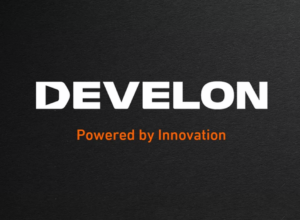
Doosan to become DEVELON!
Hyundai Doosan Infracore (HDI) have today announced their new brand name. DEVELON will replace...
Find Out More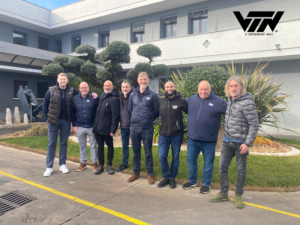
Blue Machinery become distributor for VTN attachments
We are delighted to announce that Blue Machinery and Murray Plant (A Blue Scotland Company) have...
Find Out More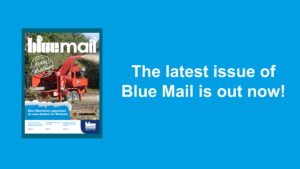

Blue Machinery appointed as new dealers for Morbark
We are delighted to announce that Blue Machinery have been appointed as the exclusive distributors...
Find Out More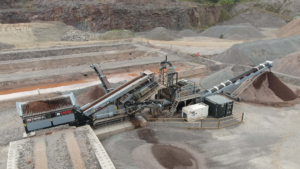
Blue Machinery expand Terex Washing Systems agreement across the UK
We are delighted to announce that both Blue Machinery (Southern) and Blue Machinery (Central) will...
Find Out More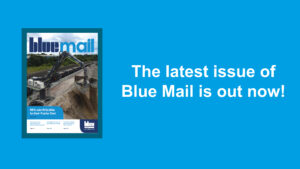
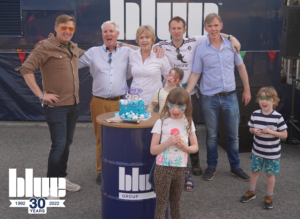
Celebrating 30 years of Blue Machinery Central
Celebrating 30 Years of Blue Machinery Central 2022 is the year that we celebrate 30 years of...
Find Out More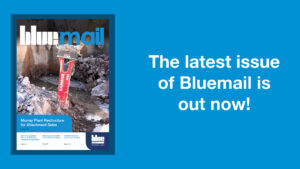
The latest edition of Bluemail is out now! Read it here.
The latest issue of Bluemail is out now! 📖 Read it...
Find Out More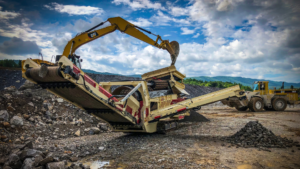
Blue Scotland to become the MDS (A Terex Brand) Distributor in Scotland & North East England
Blue Machinery (Scotland) Ltd have been appointed as the MDS distributor for Scotland and the North...
Find Out More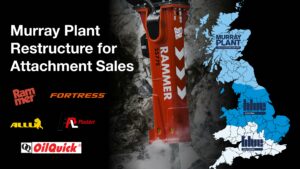
A Restructuring of Murray Plant for Attachment Sales
Since Blue Group purchased Murray Plant back in 2019, it has always been our goal to grow the...
Find Out More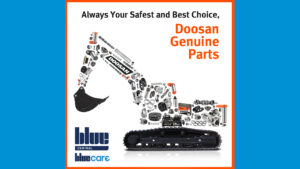
Develon Genuine Parts – Blue Central authorised Develon Parts provider for the North West & North Wales
Blue Central stock an extensive range of genuine Develon Parts at their Develon Parts Centre in...
Find Out More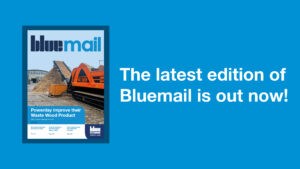
The Winter Edition of Bluemail is out now… Read it here!
Some of the highlights include: ☑️ Blue Central appointed Doosan Infracore...
Find Out More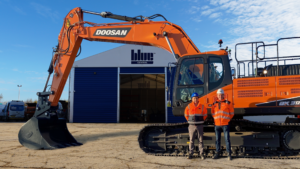
Blue Central Appointed Doosan Dealer for North West & North Wales!
Blue Machinery (Central) Ltd are delighted to announce that they have been appointed the Doosan...
Find Out More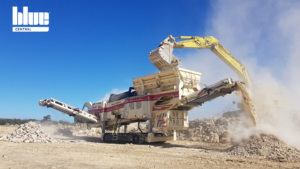
Blue Central Appointed New MDS – A Terex Brand Dealer
Blue Machinery (Central) Ltd have been appointed as the MDS distributor in northern and central...
Find Out More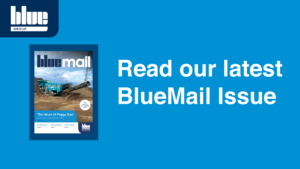
The November Edition of BlueMail is out now. Read it here!
The November edition features some great stories including: ☑️ RFS Works...
Find Out More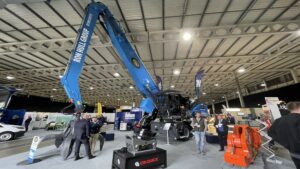
Blue Exhibit at Let’s Recycle Live/Demo Expo and CARS/ MRE
September saw the return of trade shows and exhibitions within our industries, and we were...
Find Out More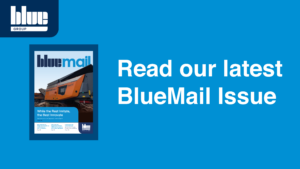
The latest BlueMail is out now. Read it here!
The June 2021 Q2 BlueMail Issue is out! For this edition we've given the magazine a bit of a...
Find Out More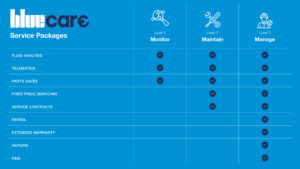
Blue Central take their aftermarket services to the next level with the launch of Blue Care
Coming into effect as of March 1st 2021, Blue Machinery Central has introduced three new aftersales...
Find Out More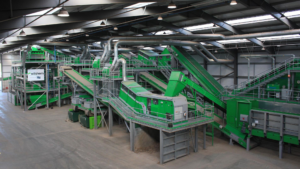
Blue complete the design & installation of a state-of-the-art MRF for Willshee’s
Blue Machinery Central are proud to announce the completion of a new state-of-the-art MRF...
Find Out More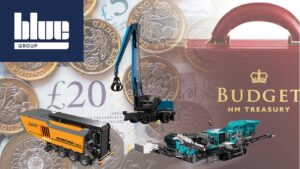
Take advantage of the Super Deduction with Blue!
During last week’s 2021 budget update Rishi Sunak announced ‘The Super Deduction’, which...
Find Out More
Blue Group Ranked 31st in The Sunday Times International Tracked 200
We are delighted to announce that we have been ranked 31st in The Sunday Times International...
Find Out More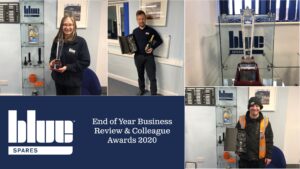
Blue Spares 2020 Business Review & Colleague Awards
Blue Spares recently held their annual business review and colleague awards for 2020, albeit this...
Find Out More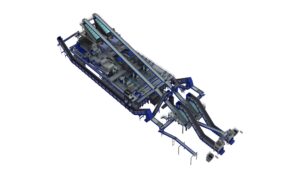
Blue Southern to supply multi-million-pound waste processing facility
Blue Machinery (Southern) Ltd has been named as preferred supplier for the multi-million-pound...
Find Out More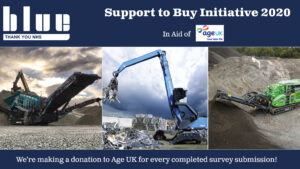
Support to Buy Initiative 2020 – Complete this short Survey and we’ll make a donation to Age UK!
Three Questions... …is all it takes to complete our survey - and we’ll make a donation to Age...
Find Out More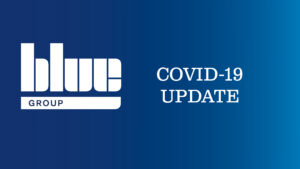
Blue Group COVID-19 UPDATE
Extra Steps we're taking... Following the ongoing development of Coronavirus, we would like to...
Find Out More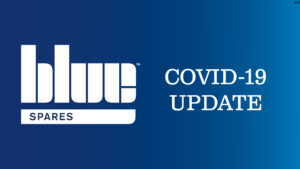
Blue Spares COVID-19 Update
We wanted to update you on steps we are taking to keep our team members and business partners safe,...
Find Out More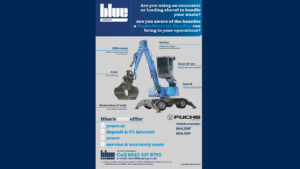
Blue Launch 2020 offer on Fuchs Material Handlers
Introducing Blue’s new 2020 offer on the Fuchs MHL 310F and 320F Material Handlers! This limited...
Find Out More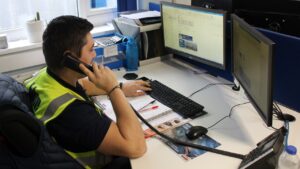
Blue Spares employee receives staff recognition award for going the extra mile
John Dennan, Senior Account Manager at Blue Spares, went above and beyond to help a desperate...
Find Out More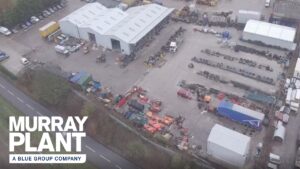
Expansion of Murray Plant continues with a new Depot and the appointment of an Operations Manager
Murray Plant, A Blue Group Company, continue their expansion plans with the opening of a Warrington...
Find Out More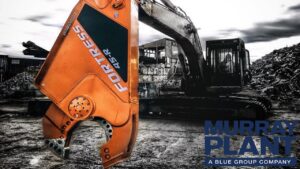
Murray Plant named as Shearcore’s Worldwide Distributor of the Year 2019
Superior, WI—ShearCore announced that Murray Plant, a Blue Group company, has been named the...
Find Out More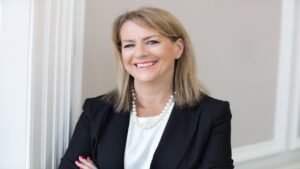
Finance Director of the Year 2019 – Susan Shardlow
On Thursday 21st November 2019, Blue attended the ‘Finance Director of the Year’ awards, at the...
Find Out More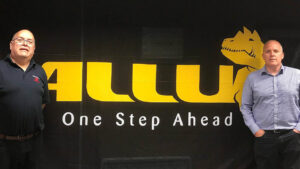
Murray Plant appointed exclusive dealer for the UK
Murray Plant Ltd, a Blue Machinery Group company, has recently been appointed ALLU’s exclusive...
Find Out More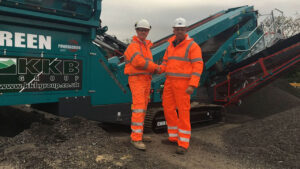
New Powerscreens Help Cut Asphalt Production Costs
Four Powerscreen Chieftain 1400 Screens have been purchased by KKB Group from Blue Machinery...
Find Out More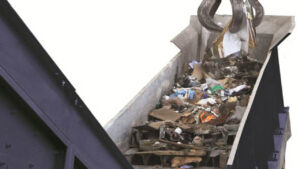
How Technology can improve recycling plants
Technology is already involved in existing recycling processes to increase speed and efficiency....
Find Out More
Why You Should Choose Genuine Crusher Spares
In order for our Blue Spares department to be as successful as it is, we rely heavily on the...
Find Out More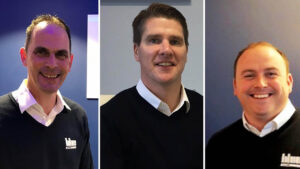
Blue Group appoints three General Managers within three of our divisions
Blue Group is delighted to announce the appointment of Ian Webber, Stuart Hardiman and Iain...
Find Out More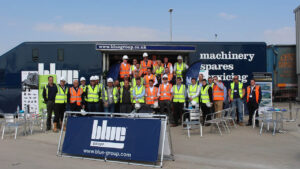
Blue Scotland Hold Successful Open Day
Blue Scotland recently held a highly successful Open Day in association with Central Demolition...
Find Out More
Blue to exhibit at Waste’17
Blue are delighted to be exhibiting at Waste’17 which is to be held on Thursday 8th June at Old...
Find Out More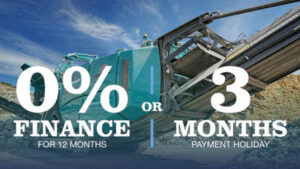
Blue Finance Offer 0% for 12 Months
Get 0% for 12 months on any hire purchase, leasing or refinancing agreement until the end of May...
Find Out More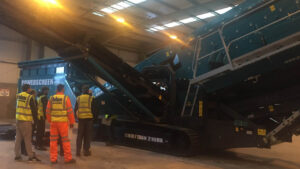
Operator Training by Blue Group
In order to continually support our customers, Blue Group have been running a number of Operator...
Find Out More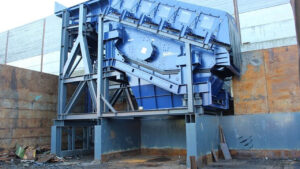
Enablelink’s SPALECK Screen Deck producing quality scrap metal
Enablelink Ltd, a well-known metal merchants formed in 2007 by Roy Millard, has just taken delivery...
Find Out More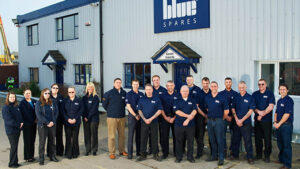
Spares in focus
In 2014 the Blue Group made the decision to form a new Spares Division with the intention of...
Find Out More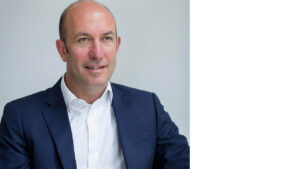
Blue Group Appoint Adrian Murphy as CEO
We are delighted to announce the appointment of Adrian Murphy as Group CEO. Working closely with...
Find Out More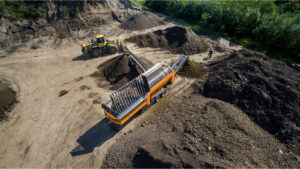
Blue Ireland announce distribution agreement with Rotobec
The relationship means that Blue will supply a range of heavy-duty attachments, used in scrap,...
Find Out More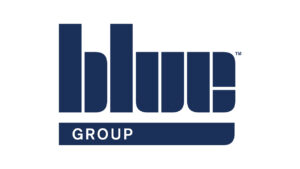
Blue Group’s Brexit Policy Statement
In order to best be prepared for the forthcoming events relating to the Brexit scheduled departure...
Find Out More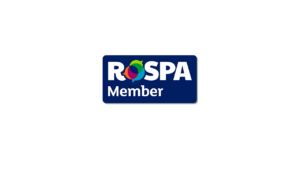
Blue Group is thrilled to announce that we are now a member of RoSPA
As a company, Blue Machinery Group is committed to the safety of its workforce and as of December...
Find Out More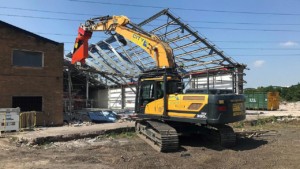
Fortress bites in the city
After a comprehensive evaluation of products, renowned Birmingham based NFDC demolition company...
Find Out More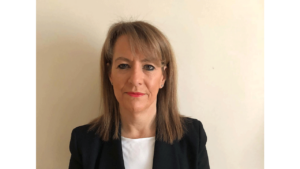
Blue Group Appoint Susan Shardlow
Blue Group are delighted to announce the appointment of Susan Shardlow as Chief Financial...
Find Out More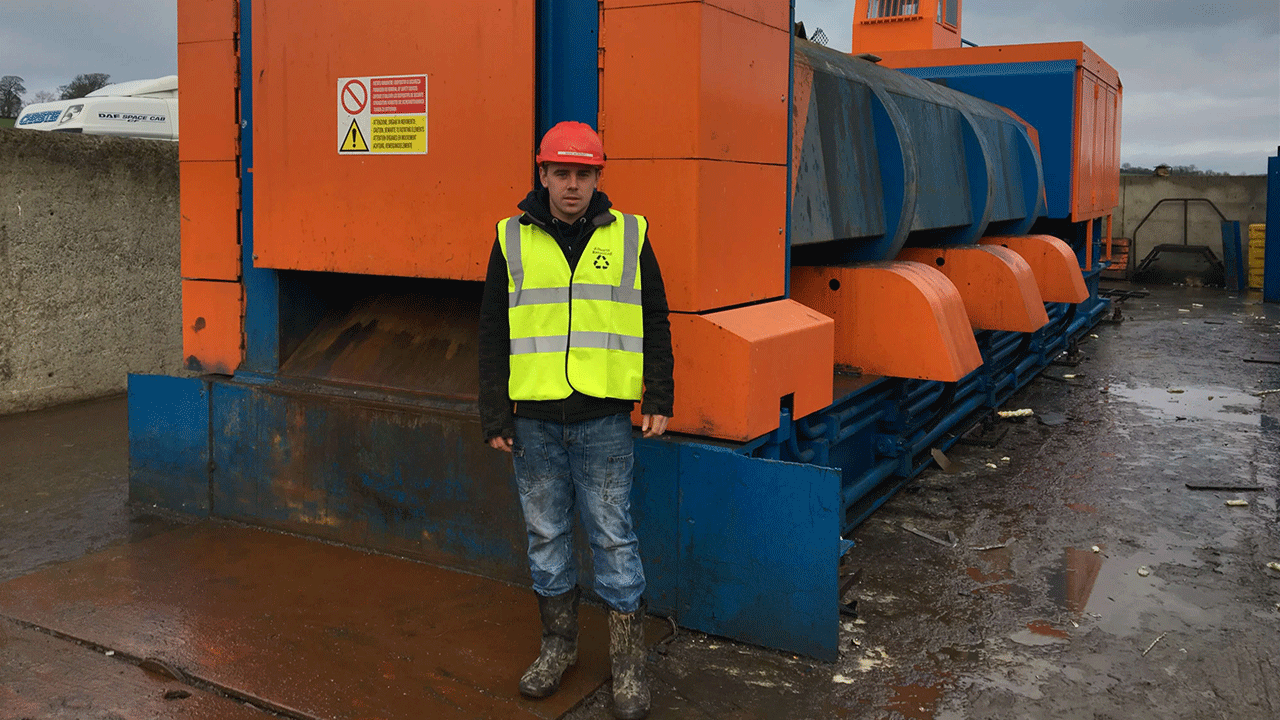
Shortts Purchase First Taurus Baler from Blue
Shortts Recycling, a family run business with a long heritage in scrap metal recycling, have been...
Find Out More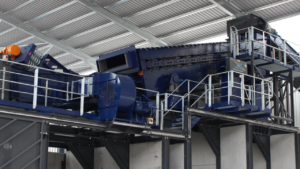
Plastic Seashores: The Importance of Recycling Plastics
With the rise in single use plastics increasing dramatically every year, an immense strain has been...
Find Out More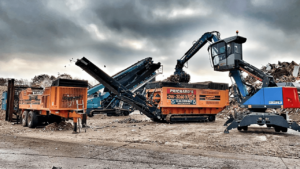
Blue Group sign distribution agreement with CK International
Blue Group have announced a new distribution agreement with CK International, a leading...
Find Out More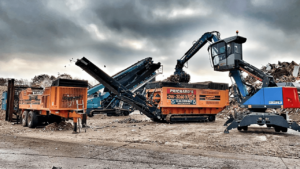
Westeria Air Density Separation Range
Separating differing types of material within a waste stream can be a challenging task which often...
Find Out More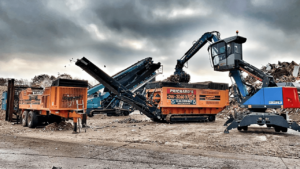
FUCHS MHL 350F
The Terex Fuchs MHL 350F is one of the most advanced machines in its class. Its state of the art...
Find Out More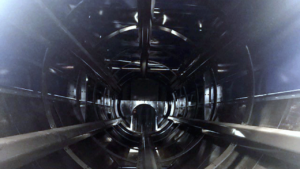
Decoding the Enigma of Plastic Codes
Plastic has become the most used material in our everyday lives. Going without it takes a huge...
Find Out More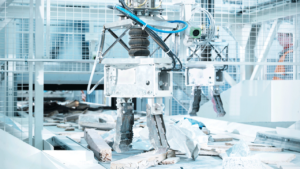
The Future of Robotic Waste Separation Technology
Technological advances in the world of waste material processing have made major strides recently,...
Find Out More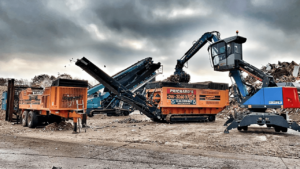
Blue Sponsored Pro Am Gets Award Nomination
A record-breaking Pro-Am golf event has been shortlisted for a major award for its contribution to...
Find Out More
Powerscreen Parts Promise
Blue Spares are delighted to introduce the Powerscreen Parts Promise offering guaranteed same day...
Find Out More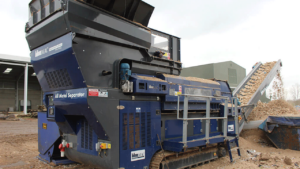
Waring Waste purchase BlueMAC All Metal Separator
When looking for a machine to help with separating ferrous and non-ferrous material from the wood,...
Find Out More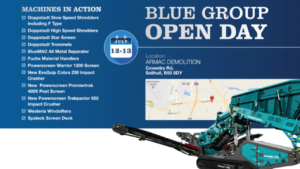
Blue Group to hold Open Day at Armac Demolition in Solihull
Blue Group will be holding a Waste Recycling Open Day on Wednesday July 12th and Thursday July 13th...
Find Out More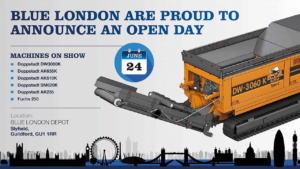
Blue London Announce Open Day
Blue London will be holding an Open Day on Saturday 24th June at their facility in Guildford,...
Find Out More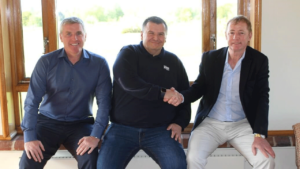
Danny Morgan to become Sales Director at Blue London
Blue Group are delighted to announce the appointment of Danny Morgan as Sales Director of the...
Find Out More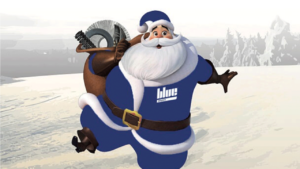
Opening Times Christmas and New Year 2016/17
Our Group offices close at differing times for Christmas. Blue Spares will remain open until...
Find Out More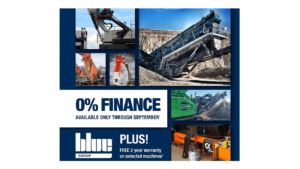
Blue 0% Finance Offer
Blue are delighted to announce that we will be running a 0% finance offer through the month of...
Find Out More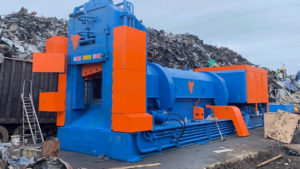
Blue Ireland deliver Taurus Shear Baler into Molloy Metals
Molloy Metals Ltd was established in 1994 by John Molloy when he purchased a mobile car crusher,...
Find Out More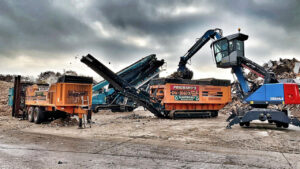
Industries That Benefit From Balers
We recently announced the distribution agreement with CK International, a company leading the way...
Find Out More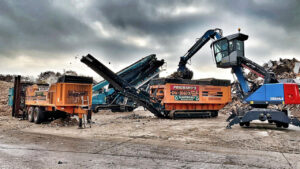
The Powerscreen Premiertrak 300/R300
Designed to exceed the primary crushing needs of customers in the mining, quarrying, and recycling...
Find Out More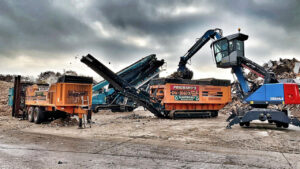
Food Waste Processing: The Cesaro Tiger HS 640
With the increasing demand for landfill space across the UK, more and more is being done to divert...
Find Out More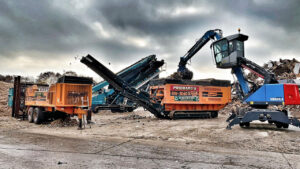
Features within the Doppstadt DW series
The DW slow speed shredder series is a powerful range of shredders used across a number of...
Find Out More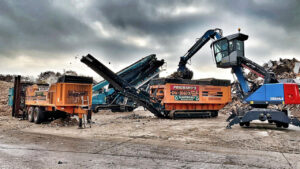
What Does The Blue Spares Service Provide?
When you rely on machines for your business to operate, break-downs bring everything to a...
Find Out More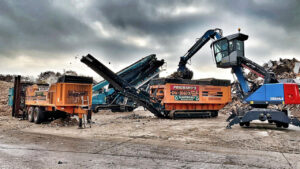
Blue Supply New £5 Million Recycling Plant
The MP for Leamington Spa and Warwick, Matt Western has formally opened Fortress Waste’s new...
Find Out More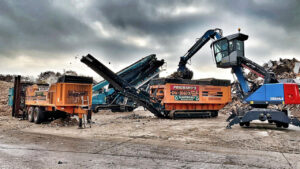
Which Everyday Products Can Be Recycled?
In the U.K we buy around 3.7 million tonnes of plastic products each and every year. With only...
Find Out More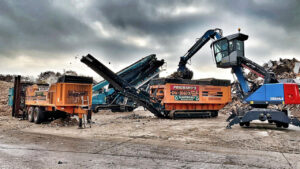
Finding the right recycling system
Every recycling operation in the UK would likely benefit from its own custom made plant...
Find Out More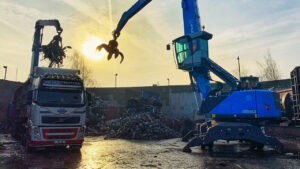
J. Davidson take on the MHL350F
Long-standing Fuchs customer J. Davidson Scrap Ltd have recently taken delivery of a new MHL350F to...
Find Out More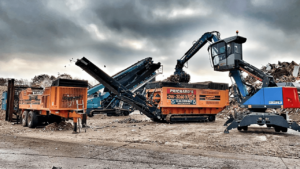
A Discussion on Recycling
Every day we are told how important it is to recycle. From magazine articles to televised...
Find Out More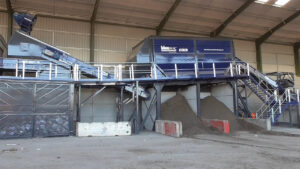
Enterprise Skiphire installs tailor-made BlueMAC recycling plant
Enterprise Skiphire has recently invested in an extremely innovative, custom made recycling plant...
Find Out More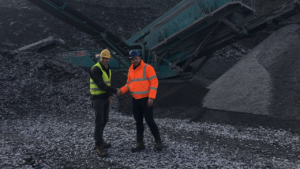
Blue Group Announces Distribution Agreement with Major Wire
Blue Group are delighted to announce an exclusive distribution agreement with Canadian Company,...
Find Out More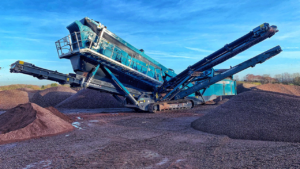
Another Mobile Screen for longstanding customer JPE Aggregates
JPE Aggregates is a midland based aggregate supplier specialising in the delivery of sand, recycled...
Find Out More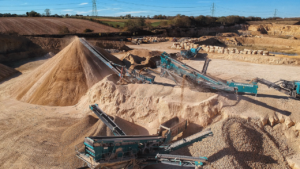
Creeton take the new Chieftain 2200
Following the purchase of a new Premiertrak 400 XA Jaw crusher in 2017, Creeton Quarry have...
Find Out More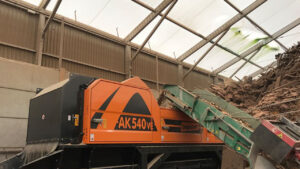
Westminster Waste invest in electric
For wood waste processing, the benefits over diesel can be substantial in certain...
Find Out More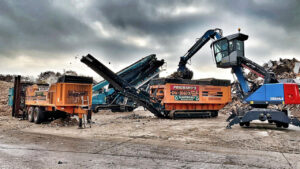
Blue Group Appoint Michael Strain
Due to strong recent growth, plant design and build specialist BlueMAC, has announced the...
Find Out More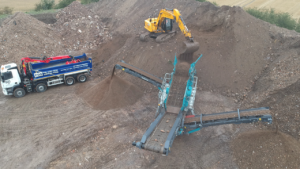
FDS Grab Hire purchase Warrior 1400X from Blue
The origins of FDS began in 2001, when business owner Franco De Simone set up FDS Building...
Find Out More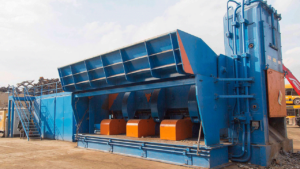
Why you should be using Taurus Bluline Shear Balers
The Taurus Bluline shear balers from Blue Group are a hugely versatile machine capable of pressing...
Find Out More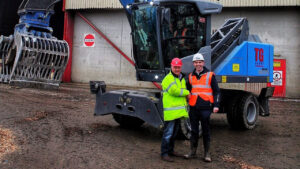
Tudor Griffiths invests in Fuchs for their recycling site in Ellesmere.
The new Fuchs MHL331 F series is the latest acquisition by the TG Enviro division, which is...
Find Out More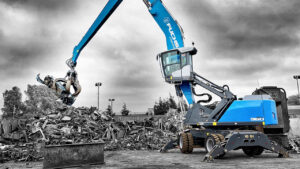
I. J. Kayes Scrap Metal Ltd. are blown away by the performance of The Fuchs’ MHL360 F
Due to increased tonnages coming in to site, and a soon to arrive new shear baler with increased...
Find Out More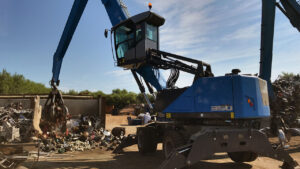
Bendall’s Metal Recycling in Gloucester takes on its second Fuchs MHL350 in less than a year
Family owned Bendall’s Metal Recycling Ltd have recently purchased their second Fuchs MHL350...
Find Out More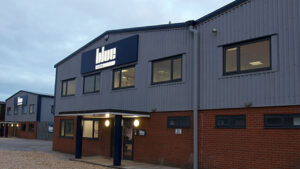
Restructuring at Blue Group
At Blue Group, we have enjoyed a significant period of success over a prolonged number of years,...
Find Out More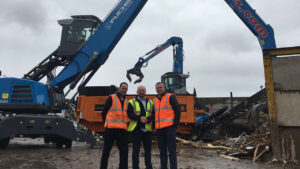
Jones Skip Hire purchase Fuchs MHL350
Blue Southern have recently delivered a Fuchs MHL350 to Jones Skip Hire. The Wolverhampton based...
Find Out More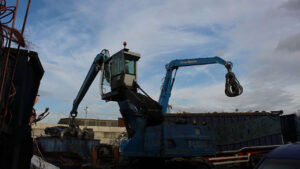
Crow Metals purchases second Fuchs Material Handler
Crow Metals, is a 4th generation family business, which was originally set up by W. Wakefield in...
Find Out More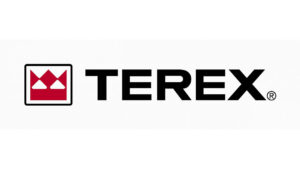
The Terex Brand: Powerscreen and EvoQuip
Blue Group is one of the UK’s biggest dealers for the Terex crushing and screening brands. The...
Find Out More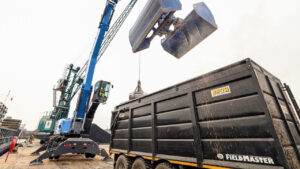
Quality Freight UK invests £700,000 in new fuchs crane
Quality Freight UK has significantly increased its cranage capability at its Ellesmere Port main...
Find Out More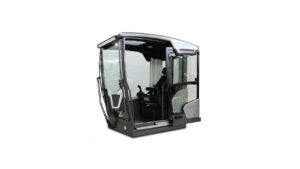
MHL390 F with New Fuchs® Cabin, Wins Prestigious Design Award
The MHL390 F with new Fuchs® cabin, won the prestigious iF Design this year. Germany’s oldest...
Find Out More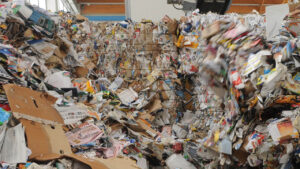
What Happens To Our Waste When We Throw It Away?
After throwing your rubbish into the bin and having it collected we don’t tend to give much...
Find Out More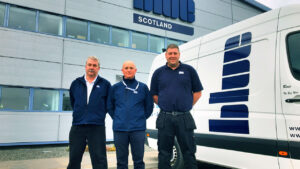
Blue Fuchs increase focus on Scottish market
Blue Fuchs, which has its head office in Portishead near Bristol, is increasing its focus on the...
Find Out More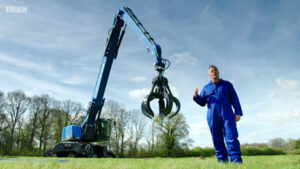
Blue Fuchs hit the target for Top Gear.
Blue Fuchs, a division of Blue Group, were recently on the receiving end of an unusual request from...
Find Out More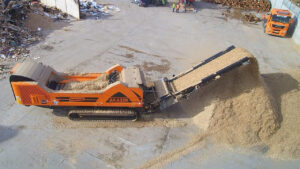
Boden Group Purchase Doppstadt High Speed Shredder
One of the UK’s biggest and most established wood waste recyclers, The Boden Group, have recently...
Find Out More
Let’s Talk About Wood Shredders
At Blue Group we pride ourselves on our vast range of material processing equipment, which is...
Find Out More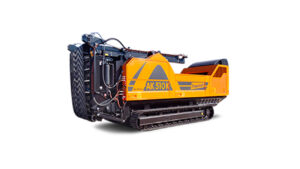
Wood Shredders and Chippers: Economical Applications
In the recycling industry companies are always looking for ways to recycle more. With the demand...
Find Out More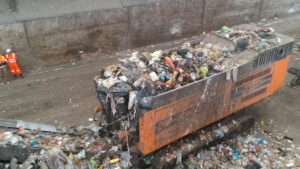
WSR Recycling’s Doppstadt 3060K processes an epic 100 tonnes per hour
WSR Recycling have upgraded to a Doppstadt DW 3060K BioPower Shredder following expansion at their...
Find Out More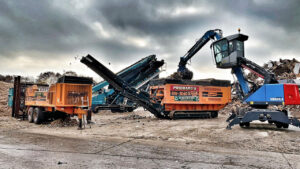
Blue is a one stop shop for Prichard’s Contracting
Prichard’s Contracting takes advantage of being able to purchase all their wood recycling...
Find Out More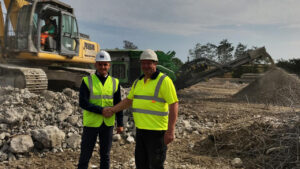
Derby Crushing and Screening purchase the impressive EvoQuip Cobra 230 Impactor.
Derby Crushing and Screening have purchased an EvoQuip Cobra 230 Impactor crusher from Blue to...
Find Out More
EvoQuip Cobra 230 The perfect solution for Cornish Roads
Mark Coad purchases the first EvoQuip Cobra 230 impact crusher in the Southwest of England supplied...
Find Out More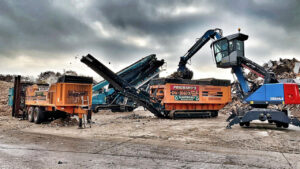
The Metrotrak doubles production rate for Dolan Skips
Dolan Skip Hire was established by Kieran Dolan and his wife Theresa Dolan in 2007. Over the years...
Find Out More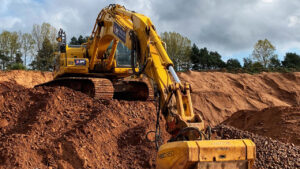
When there’s no space for a full-size crusher, a Hartl HBC 950 Crusher Bucket is just the job for JPE Aggregates.
JPE is one of the Midlands leading suppliers of aggregates, sand and soils to the construction...
Find Out More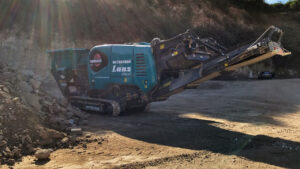
New Powerscreen Metrotrak for Lanz Group
Leading Waste Management Company Lanz Group, who have various sites in Berkshire as well as two in...
Find Out More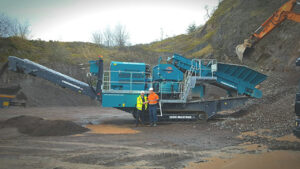
Three Major Scottish Customers Choose Powerscreen for the First Time
Grange Quarry, Barrachander Quarry and Miller Plant have recently chosen Powerscreen equipment for...
Find Out More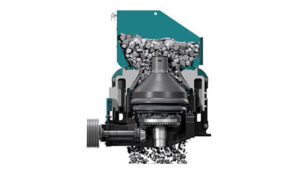
Cone Crusher Applications
You will usually find cone crushers in a number of industries that revolve around mining,...
Find Out More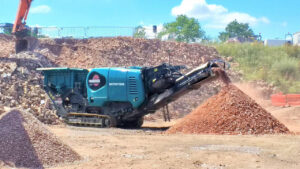
The Metrotrak HA Jaw Crusher by Powerscreen
The Powerscreen crusher range from Terex including; mobile jaw crushers, cone crushers and impact...
Find Out More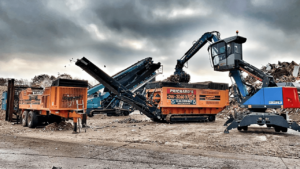
The Machinery Debate: New or Used
The discussion that depicts second hand items and brand new items against one another can be...
Find Out More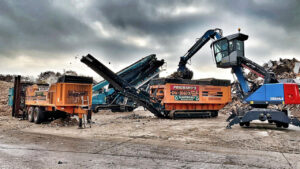
Crusher Types
Blue Group supply world leading materials processing equipment for a wide variety of different...
Find Out More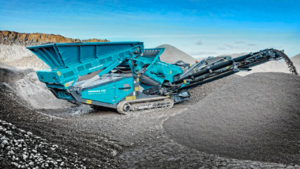
Blue Central Expand Powerscreen Territory
With over 50 years powering the industry, Powerscreen has developed and maintained an aggressive...
Find Out More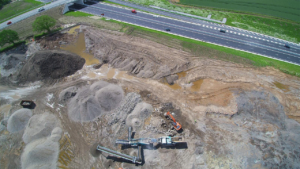
Powerscreen Premiertrak R400 and Warrior 1400X assist with £192 million bypass
The Premiertrak R400 mobile jaw crusher and Warrior 1400X mobile screen were cleaning up the...
Find Out More
Blue to attend Demolition Expo 2017
Blue are delighted to be attending Demolition’s biggest event on 22nd - 24th June at Herts...
Find Out More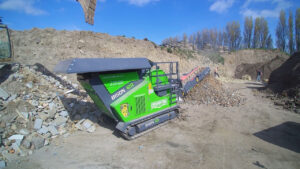
Crushintons Ltd take first ever EvoQuip machine in the South East
Crushintons Ltd, based in Kent have recently purchased a new Bison 120 Jaw Crusher from Blue...
Find Out More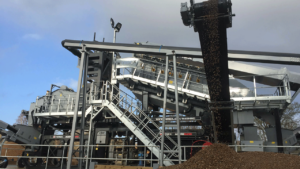
Leiths Take Second Aggresand 165 Wash Plant from Blue Scotland
The Leiths Group, a multi-discipline organisation and one of Scotland’s largest, privately owned...
Find Out More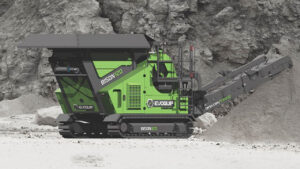
Blue Central to Exhibit at Lamma 2017
Blue Machinery Central will be exhibiting at the Lamma event The event is to take place on...
Find Out More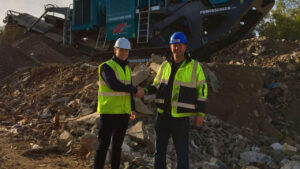
Britaniacrest Recycling Goes Blue Again with Mobile Jaw Crusher
Britaniacrest Recycling Ltd, a family business formed in 1993 by Ray Foss Snr and with three sites...
Find Out More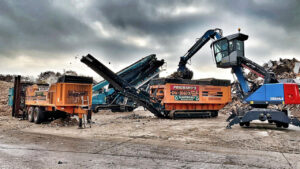
Leiths take delivery of seven Powerscreen Mobile Crushing and Screening Plants
Leiths (Scotland) Ltd, a multi-discipline organisation and one of Scotland’s largest, privately...
Find Out More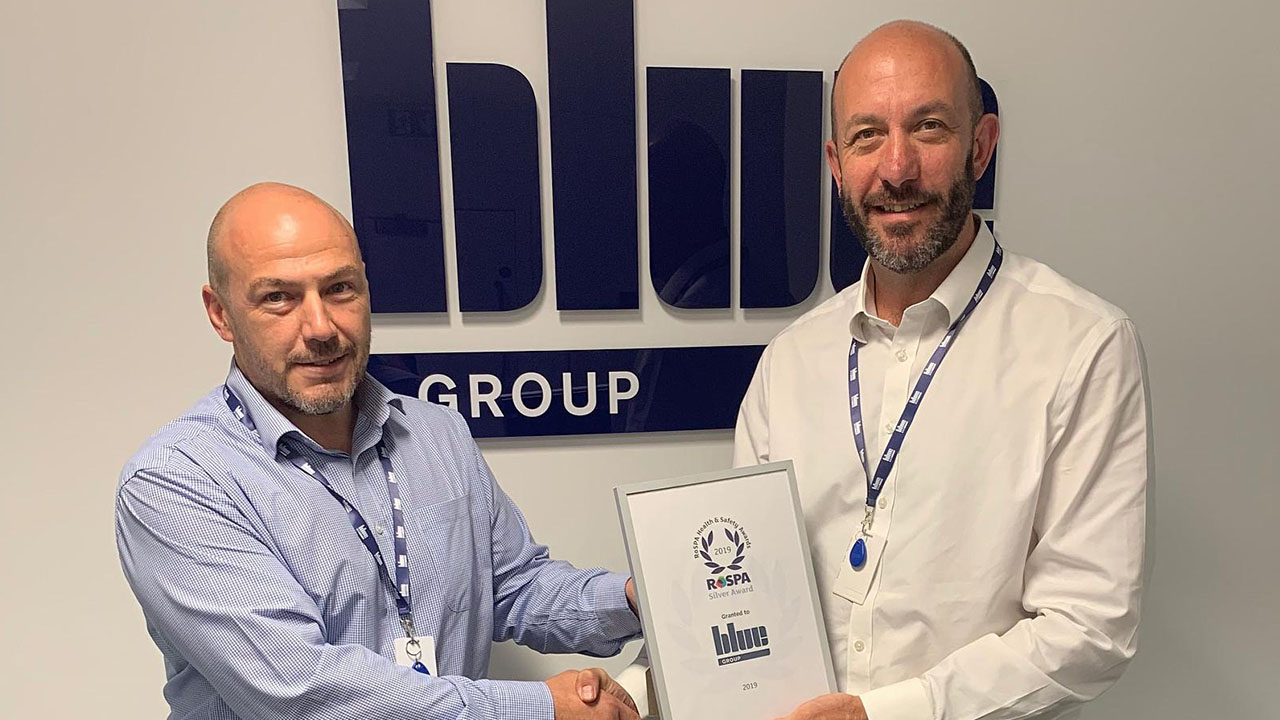
Blue handed RoSPA 2019 Silver Award
Blue Machinery (Group) Ltd has achieved a Silver in the internationally-renowned RoSPA Health and...
Find Out More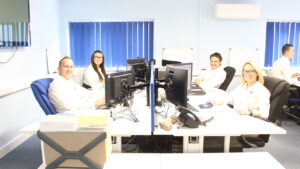
Blue Spares invest to further strengthen customer support
As part of the ongoing investment in our Group infrastructure, Blue Spares has recently gone...
Find Out More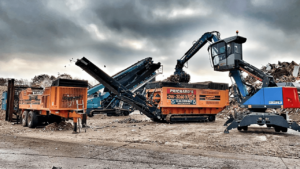
Blue Group demonstrate a range of new equipment at Open Day
Blue Group recently held a highly successful open day The event was held over two days in July,...
Find Out More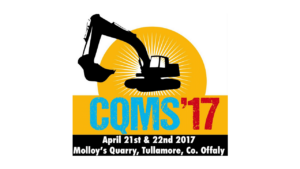
Blue Ireland to exhibit at CQMS
Blue Machinery Ireland, part of Blue Group will be exhibiting at this year’s CQMS. The business...
Find Out More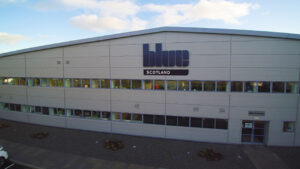
Blue Scotland Announce Open Day
Blue Scotland will be holding a Waste Recycling Open Day on Thursday May 11th and Friday May 12th...
Find Out More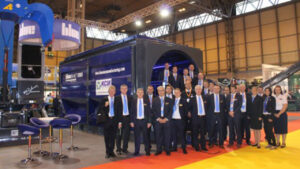
RWM a huge success for Blue Group
Since Blue Group was formed eleven years ago, the company has always been a major exhibitor at the...
Find Out MoreBlue Group Become UK Distributor for Fortress Shears
Following on from their recent acquisition of Murray Plant, Blue Group have announced an agreement...
Find Out More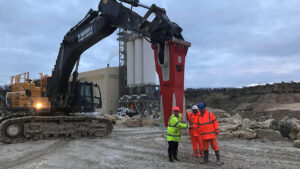
D Wardle (Plant) Ltd Purchase Rammer’s Latest and Biggest Hammer.
Murray Plant have recently delivered a 9033 hydraulic Rammer Hammer to D Wardle (Plant) Ltd. The 7...
Find Out More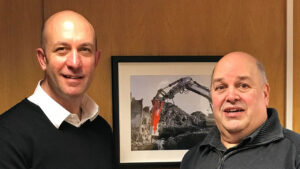
Blue Purchase Murray Plant
Blue Group have announced the purchase of Murray Plant, the Rammer distributor for the...
Find Out More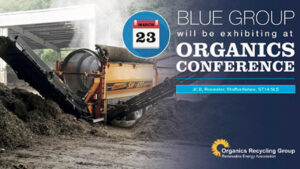
Blue to Exhibit at the Organics Conference
Blue are delighted to be exhibiting at Organics Recycling 2017 which is to be held at JCB,...
Find Out More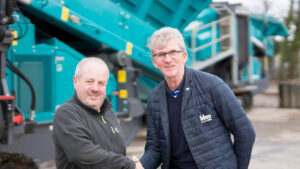
KJ Crushing Ltd. take 9th Powerscreen
KJ Services located in South Wales have ordered a further three Powerscreen machines, following the...
Find Out More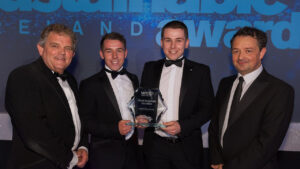
BlueMAC Awarded for its Manufacturing Innovation
BlueMAC Manufacturing has been rewarded at the annual Sustainable Ireland Awards for innovation in...
Find Out More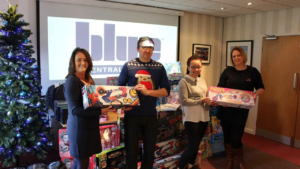
Central create Christmas cheer
Blue Central have donated over £2,000 worth of toys and gifts to a local charity, in preference to...
Find Out More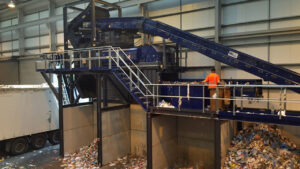
Falkirk Council are leading the way with a BlueMAC waste recycling plant
The aim is to recycle over 70% of the collected household material, with a maximum of just 5% going...
Find Out More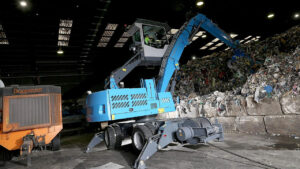
Ireland’s First Electric Fuchs Materials Handler Goes To RiverRidge Recycling
RiverRidge Recycling has just taken delivery of Ireland’s very first electrically powered Fuchs...
Find Out More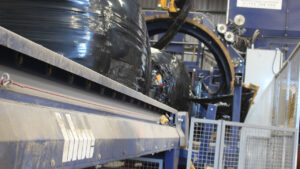
Furnishing Frimstone
Frimstone Limited, which has 13 sites throughout East Anglia recently approached Blue Central to...
Find Out More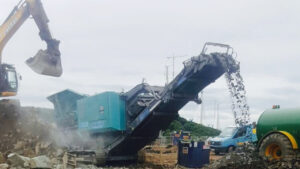
George Beattie and Sons Ltd choose an R400 mobile jaw crusher
Blue Machinery Scotland has delivered a Powerscreen Premiertrak R400 Pre Screen mobile jaw crusher...
Find Out More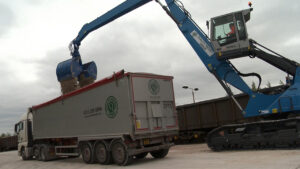
Blue Fuchs Supply Quality Freight UK With Two New Fuchs Material Handlers
Blue Machinery Fuchs have recently sold two new material handlers to Quality Freight UK as the...
Find Out More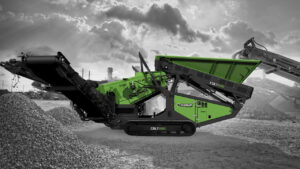
Blue to Supply EvoQuip throughout the UK
Blue have become the exclusive supplier for EvoQuip. This new range from Terex offers a...
Find Out More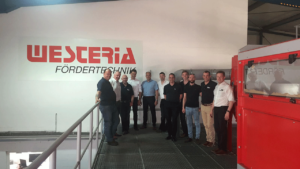
Blue Group Announce Exclusive UK Agreement with Westeria
Blue Group are delighted to announce that an exclusive distribution agreement for the UK and...
Find Out More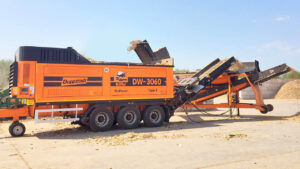
The New DW 3060 F Type Waste and Wood Shredder from Doppstadt
The new Doppstadt slow speed waste and wood shredder with innovative shredding system Doppstadt...
Find Out More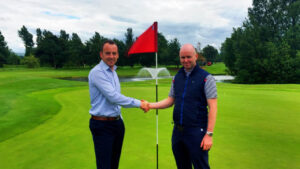
Blue Ireland Sponsor Prestigious Killeen G.C. Pro-Am
Blue Machinery Ireland have been confirmed as the new headline sponsor for prestigious Killeen...
Find Out More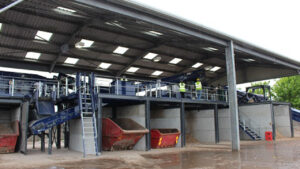
New Fines Clean Up Plant at Lowmac
Lowmac Waste & Recycling has invested in an extremely versatile, tailor-made recycling plant to...
Find Out More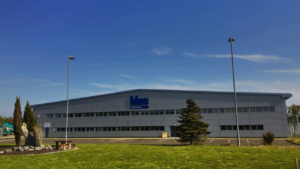
Scotland Makes its Move
Blue Scotland has recently moved to a 3.5 acre facility, incorporating newly renovated office...
Find Out More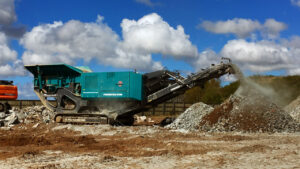
Two PT R400 Mobile Jaw Crushers bought to crush foundations
ADM Regeneration based in Lymm, was formed in 2011 by current owner Adam Matthews, undertaking...
Find Out More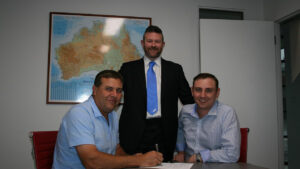
BlueMAC Spreads Its Wings!
BlueMAC is now pleased to announce that it has appointed SKALA Australasia Pty Ltd as the exclusive...
Find Out More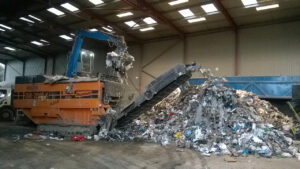
The Quest for Zero to Landfill
Blackpole Recycling, based in Worcester, have recently purchased a Fuchs MHL 250 and a Doppstadt...
Find Out More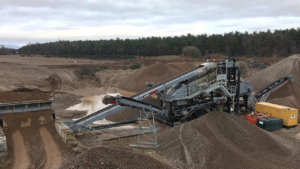
New Modular Wash Plant for Breedon Aggregates
Breedon Aggregates has installed a Terex® Aggresand 165 Wash Plant at their Capo Quarry, Edzell,...
Find Out More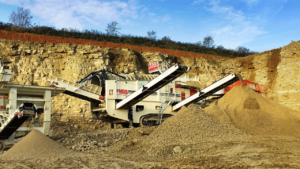
Probably the World’s Largest Mobile Trommel Goes to Gallagher Aggregates
Following an extensive and successful demonstration at Gallagher Aggregates’ Hermitage Quarry,...
Find Out More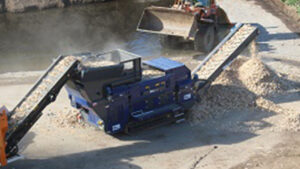
BlueMAC All Metal Separator
Available in tracked, static or skid variations. Boost your profit with contamination free...
Find Out More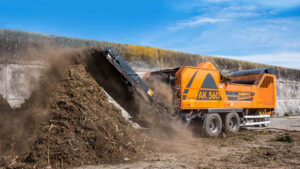
Doppstadt Launch AK560 waste and wood shredder
Due to the exceptionally high demand for the Doppstadt AK 510 shredder over the last few years, the...
Find Out More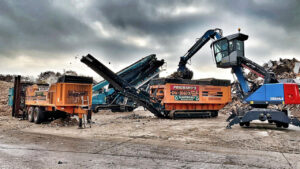
The New SM 620 SA mobile trommel screen available from January 2016
Testing of the new SM 620 SA mobile trommel screen prototype has now been completed meaning that...
Find Out More
Incredible year for Blue Group
Blue Group have had an amazing year. Starting with new offices opening in Portishead, near Bristol,...
Find Out More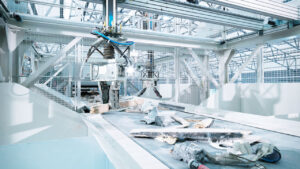
Blue Group and ZenRobotics announce distribution agreement for the UK
Blue Group are delighted to announce that a distribution agreement for the UK and Ireland has been...
Find Out More
Biggest Ever Plant for BlueMAC Designed and built for Irish Waste in Carryduff, Belfast
BlueMAC’s largest plant to date, designed and built for Irish Waste, has recently started to...
Find Out More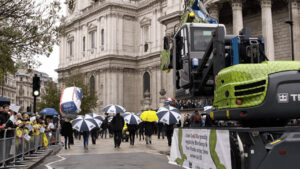
Scaling it up at the London Lord Mayor’s Show.
A rainy 14th November 2015 saw Blue taking part in the 800th London Lord Mayor’s Show, with the...
Find Out More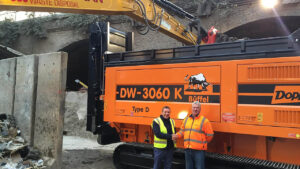
O’Donovan’s take 3 of the best from Blue London
O’Donovan Waste Disposal Limited is one of London’s leading independent waste management and...
Find Out More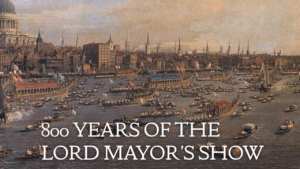
Blue Group at Lord Mayors Show 2015
The Blue Group are taking part in this year’s London Lord Mayor’s Show procession which takes...
Find Out More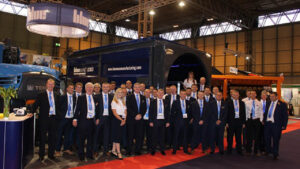
Blue Steals the Show at RWM
Blue again wowed visitors at this year’s RWM exhibition held at the NEC in Birmingham. The 430sqm...
Find Out More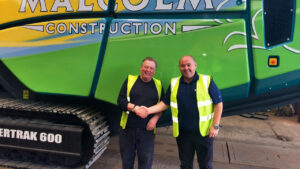
Premiertrak 600 Mobile Jaw Crusher
Malcolm Construction take delivery of the new Powerscreen Premiertrak 600 Mobile Jaw...
Find Out More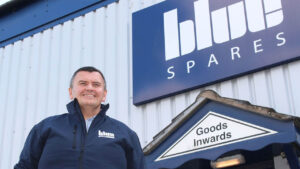
Danny Morgan becomes part of the Blue Team
Blue Group are delighted to announce the appointment of Danny Morgan as Export Sales...
Find Out More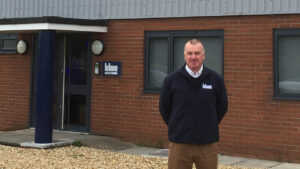
Tony Weir joins Blue as Technical Director
With his 25 years’ experience in the crushing and screening industry, along with a certified...
Find Out More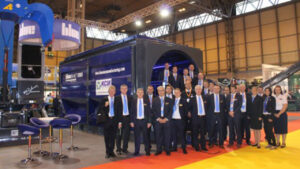
Blue at RWM Exhibition – 15th – 17th September 2015
Blue will again be exhibiting at this year’s RWM exhibition, which is to take place between...
Find Out More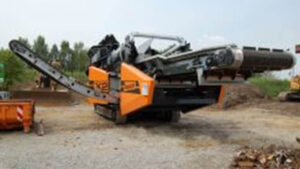
Doppstadt Expo
Doppstadt recently celebrated their 50th Anniversary with an incredible EXPO, attracting over 3,000...
Find Out More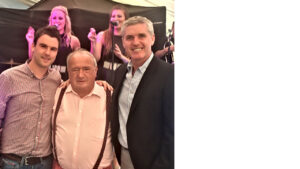
John Wade Celebrates 50 Years in Business
Longstanding Blue Scotland customer, John Wade Group recently celebrated their 50th anniversary at...
Find Out More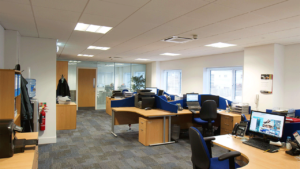
New offices for Blue Southern and Blue Fuchs
An £800,000 refurbishment of both the Blue Fuchs and Blue Southern offices in Portishead has...
Find Out More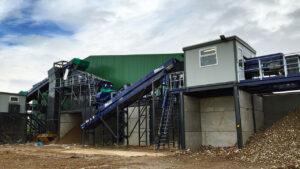
BlueMAC MRF Installed for Murray Browns
Murray Browns is an independent, family-owned company headquartered in Flixton, near Scarborough,...
Find Out More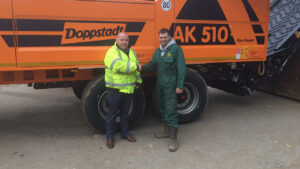
High Speed upgrade for McKenzie
Prominent Scottish wood recyclers, M Mckenzie Old Pentland LLP have recently taken delivery of...
Find Out More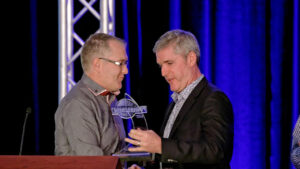
Blue Machinery Scotland Named “World Dealer of the Year” at Powerscreen World Dealer Conference
Blue Machinery (Scotland) Limited is proud to announce that the company has received the highest...
Find Out More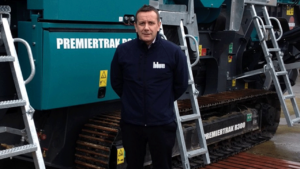
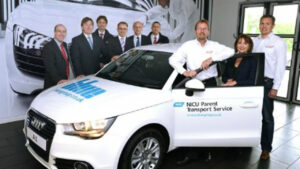
Blue Southern support NICU Charity
Blue Group are delighted to support NICU, a charity that is close to all our hearts. Blood Bikes...
Find Out More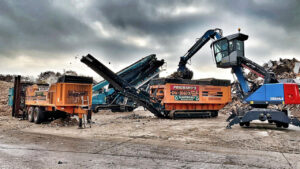
Season’s Greetings from Blue
The team at Blue Group would like to wish you a very Merry Christmas and a healthy, happy,...
Find Out More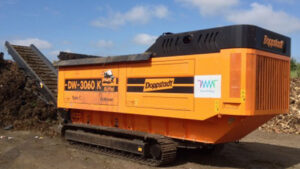
Tamar Organics Takes Delivery of Two More Doppstadt Machines
Tamar Organics has purchased a Doppstadt DW 3060K Bio Power shredder and a Doppstadt SM 620K...
Find Out More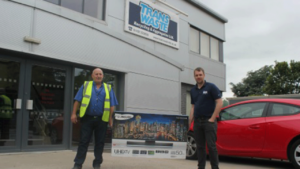
Transwaste score in Blue Spares Promotion
Bruce Pritchard of Transwaste Recycling and Aggregates was the lucky winner of Blue Spares latest...
Find Out More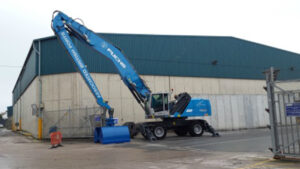
ABP Teignmouth add to Fuchs fleet
Blue Fuchs have once again supplied a Fuchs material handler to the UK's leading ports group,...
Find Out More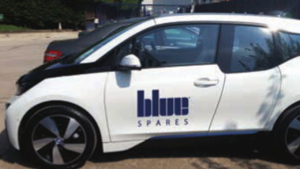
Blue Spares show their true colours
Lots of companies talk the talk but do they actually walk the walk? Blue Spares has introduced its...
Find Out More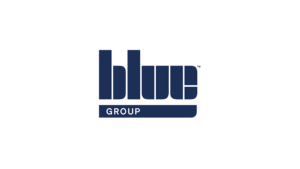
BlueMAC Achieves ISO Quality Management Accreditations
Specialist bespoke recycling plant manufacturer, BlueMAC, has achieved two stringent ISO quality...
Find Out More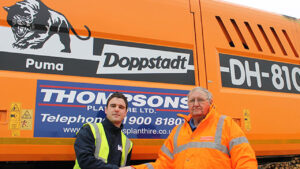
Thompsons Plant Hire Continues Allegiance to Blue Machinery
Thompsons Plant Hire, of Maryport, Cumbria, has purchased another Doppstadt machine from Blue...
Find Out More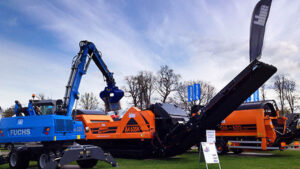
Hugely successful Scot Plant for Blue Scotland
Blue Scotland are delighted to announce another hugely successful Scot Plant exhibition. The...
Find Out More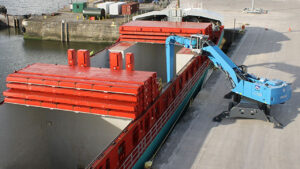
Port of Workington takes Specialist Fuchs Materials Handler
One of the UK’s fastest growing ports, the Port of Workington in West Cumbria, has further...
Find Out More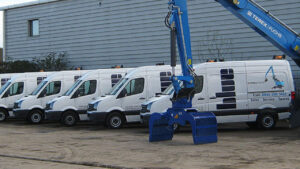
New fleet of vehicles for Blue Fuchs
After another successful year as an accredited Terex Fuchs Three Crown distributor, Blue Machinery...
Find Out More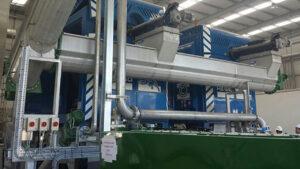
ReFood install two Tigers in Widnes
Blue Machinery (Central) are fortunate to be part of the most exciting Biogas Plant the UK Waste...
Find Out More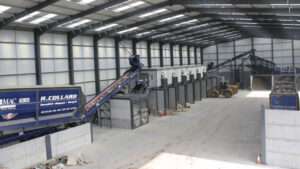
R.Collard Limited installs bespoke MRF from BlueMAC
Leading manufacturing company BlueMAC has designed and built another tailor-made installation; this...
Find Out More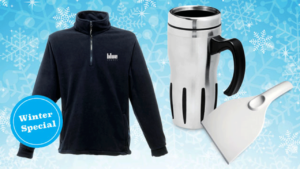
Have you got your Winter Blues?
Keep yourself warm this Winter with Blue Spares. For a limited time only, all orders placed over...
Find Out More